Filament Deposition Modeling (FDM) has revolutionized the way we think about manufacturing, prototyping, and product development. As this additive manufacturing technique continues to evolve, the emergence of specific models, components, or systems within the domain often marks a leap forward in efficiency, precision, and versatility. One such milestone is TGD170.FDM.97 – a designation that is increasingly being associated with innovation and reliability in the world of 3D printing. Whether you’re a seasoned engineer, a product designer, or a curious enthusiast, understanding what TGD170.FDM.97 brings to the table is essential for staying ahead in the additive manufacturing industry.
This article delves deep into the structure, significance, performance, and implications of TGD170.FDM.97, unpacking why it is regarded as a benchmark in the ever-growing world of Filament Deposition Modeling.
Understanding FDM: The Foundation
What Is Filament Deposition Modeling?
FDM is one of the most widely used 3D printing techniques, known for its accessibility and efficiency. It involves extruding thermoplastic filament through a heated nozzle to build objects layer by layer. The process is driven by computer-aided design (CAD) files, and it provides a low-cost, quick-turnaround solution for both functional and aesthetic prototypes.
FDM’s popularity stems from its simplicity, scalability, and the diversity of materials that can be used, including PLA, ABS, PETG, and even carbon-fiber-infused filaments. However, like all manufacturing methods, FDM has had its limitations in terms of resolution, mechanical strength, and repeatability – all areas where innovations like TGD170.FDM.97 seek to bring enhancements.
The Rise of TGD170.FDM.97
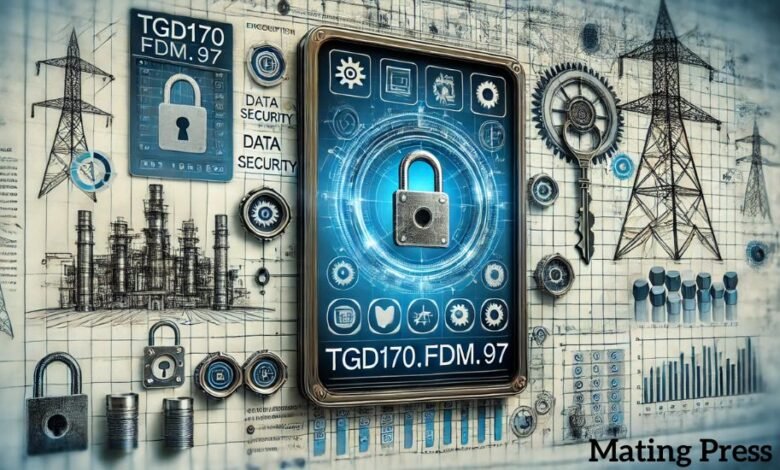
Decoding the Name
The nomenclature TGD170.FDM.97 might appear cryptic at first, but it follows a structured taxonomy. “TGD” could stand for a proprietary development series or technical guideline document. The number “170” might refer to a specific build plate size or a versioning code. “FDM” clearly aligns it with Filament Deposition Modeling, while “97” could denote a design version, year, or internal model iteration. Though the exact origin of the name may vary depending on the organization using it, the designation has become synonymous with high performance in FDM systems.
Why It Stands Out
TGD170.FDM.97 is not just another printer or filament. It represents an integrated system or standard that elevates FDM to a new level. Its distinction lies in:
- Enhanced Precision: With micro-layering capabilities as fine as 50 microns, it significantly reduces the need for post-processing.
- Optimized Extrusion System: It includes advanced nozzle design and filament feeding mechanisms that minimize clogging and maximize flow consistency.
- Thermal Regulation: Equipped with intelligent heating and cooling controls that adapt in real time to environmental conditions.
- Material Compatibility: Supports a wide range of thermoplastics and composite filaments without needing hardware changes.
- Software Integration: Comes with predictive calibration and self-diagnostic tools, often AI-enhanced, to reduce human error.
Technological Innovations Behind TGD170.FDM.97
High-Resolution Printing
A primary highlight of TGD170.FDM.97 is its capacity for ultra-fine resolutions. Unlike conventional FDM printers that often max out at 100 microns, this system enables prints as detailed as 50 microns or better. Such fine detailing is vital for sectors where aesthetics and functional accuracy are paramount, such as biomedical device prototyping and aerospace component fabrication.
Adaptive Nozzle System
Traditional FDM printers struggle with varied filament types due to rigid nozzle configurations. TGD170.FDM.97 integrates a smart nozzle system capable of adjusting temperature and extrusion speed dynamically, depending on filament type and print geometry. This reduces warping, enhances bonding between layers, and significantly improves print integrity.
AI-Driven Print Optimization
Another key feature that sets TGD170.FDM.97 apart is its integration with AI-based software systems. These tools analyze CAD designs before printing, recommending optimizations to reduce material usage and strengthen structural weak points. During printing, embedded sensors relay real-time data to ensure consistency, reducing print failures and resource wastage.
Modular Design and Scalability
Designed for flexibility, TGD170.FDM.97 systems can be easily scaled for industrial applications or compacted for desktop use. Modular components allow users to upgrade extruders, add heated chambers, or even automate filament spooling without replacing the entire unit.
Applications and Use Cases
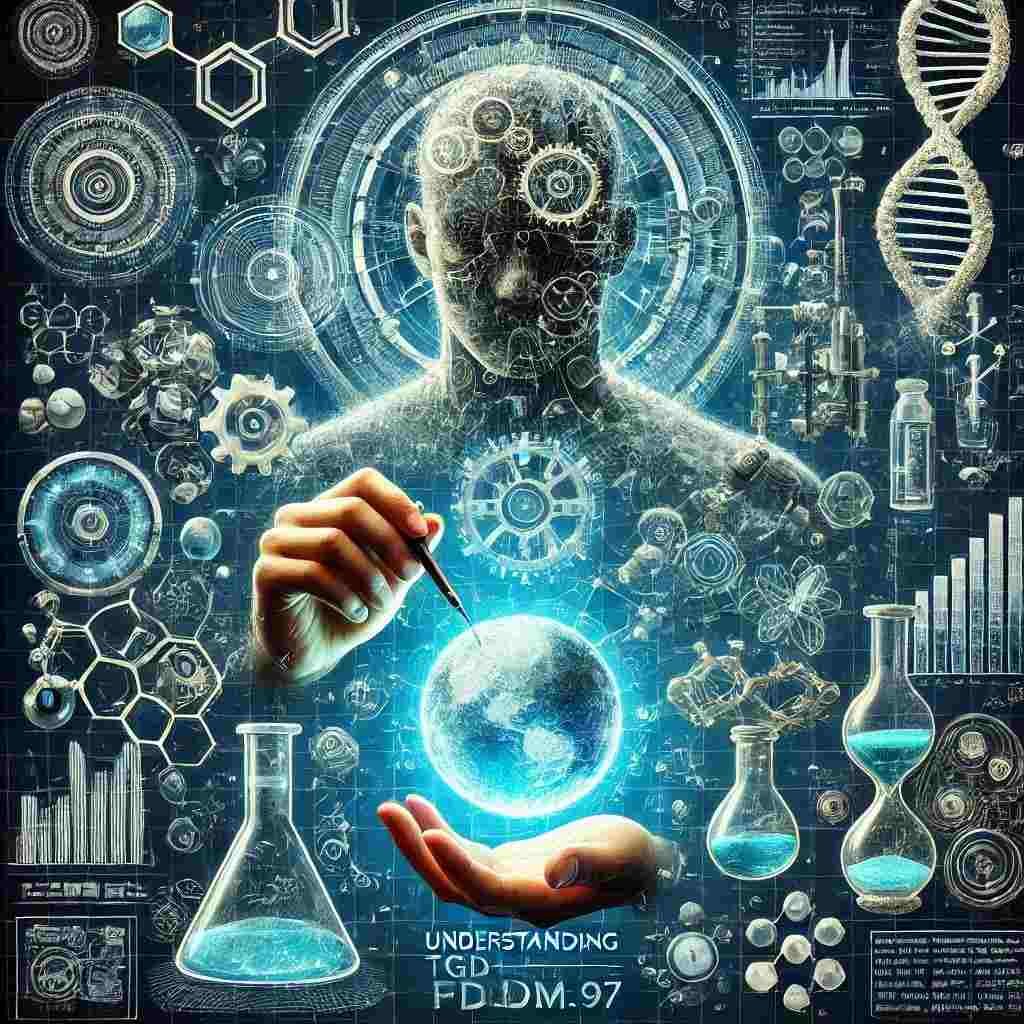
Industrial Prototyping
With the improved reliability and accuracy offered by TGD170.FDM.97, engineers and designers can develop functional prototypes that closely resemble final products. This reduces turnaround times in R&D cycles, saves costs, and speeds up product launches.
Custom Manufacturing
In sectors like healthcare, where custom solutions are often needed (e.g., prosthetics or dental models), the precision and adaptability of TGD170.FDM.97 make it an ideal tool. Its compatibility with biocompatible filaments adds another layer of applicability.
Aerospace and Automotive Parts
Weight optimization and part durability are key in these sectors. The AI tools within TGD170.FDM.97 enable lightweight yet strong designs. Add to that the ability to use engineering-grade materials, and the system becomes indispensable for fabricating brackets, housings, and structural supports.
Education and Research
TGD170.FDM.97’s intuitive interface and diagnostic tools make it ideal for educational institutions and research labs. It allows students and researchers to focus on innovation rather than troubleshooting, thereby promoting faster learning and experimentation.
Market Impact and Industry Reception
Setting a New Standard
Since its emergence, TGD170.FDM.97 has been recognized across industry forums and trade shows for setting a new benchmark in FDM capabilities. Manufacturers are beginning to adopt it not just for the technical advantages but also for the long-term cost efficiencies it promises.
Competitive Edge
Compared to contemporaries, the TGD170.FDM.97 offers a competitive edge through its combination of AI, modularity, and superior build quality. This makes it a preferred choice for companies looking to future-proof their additive manufacturing capabilities.
Sustainability Considerations
With increased global emphasis on sustainable manufacturing, TGD170.FDM.97 contributes by minimizing material wastage, enabling biodegradable filament usage, and supporting closed-loop recycling systems. This aligns with modern ESG (Environmental, Social, Governance) goals that many companies now prioritize.
Challenges and Limitations
While TGD170.FDM.97 is revolutionary, it’s not without challenges. The initial cost can be a barrier for smaller operations. Additionally, the learning curve for fully leveraging its AI features may require training. However, these drawbacks are generally outweighed by the system’s long-term benefits and robust support infrastructure.
Conclusion
TGD170.FDM.97 stands as a milestone in the evolution of Filament Deposition Modeling. Its contributions in terms of precision, adaptability, and intelligence make it more than just a product – it’s a paradigm shift in 3D printing. Whether you’re involved in industrial production, education, healthcare, or creative design, integrating a system like TGD170.FDM.97 can transform your approach to manufacturing.
As additive manufacturing continues to mature, models like TGD170.FDM.97 will serve as the benchmark for innovation. By addressing past limitations and incorporating futuristic features, it ensures that FDM remains a relevant and powerful tool in modern engineering and design.
Read more: Software UPA Explained: A New Era in Platform Architecture